Do This to be more efficient, make your team happier, and improve your results
by ActionCoach Shaun Shoenmaker
I was volunteering at St. Philips Community Center and School when I noticed something they were doing that is beneficial in many ways for small business. There were a bunch of us there giving our time towards packing up about 50,000 meals for hungry children around Dallas. We did this by forming an assembly line that separated and assigned different tasks to different people. We had some folks putting ingredients into packages, some would weigh the packages, some would seal the packages, and finally others would box the packages. There were some adjustments that had to make along the process to get the food packages correct and ready for delivery. For example, when the people weighing the packages had a package that was too heavy, they had to correct the amount of food and pour some of it out. And when the package was too light, they had to add some additional food. Well, this took additional time for the weighing team and became a bit annoying and frustrating to continue seeing inconsistent results from the ingredients team that they had to correct each time.
As the process started taking place over several packages, I noticed an interesting development. The weighing team started to notice whether there was a tendency for the ingredients team to make packages that were either too heavy or too light. Since the ingredients team was just one step in front of them in the process—in other words they were physically right next to them in the assembly line—they started to provide feedback to them as to whether they needed to make the packages heavier or lighter. Guess what happened after the ingredients team got some feedback. We started getting much better results! In fact, we had about ten packages in a row that were not only within the allotted weight range but had the exact same weight!
What were some of the benefits of this feedback? It gave us a shorter cycle time because the weighing team didn’t have to correct as many packages that were over or under weight. The feedback also boosted morale because the people at the front of the assembly line weren’t anxious about their performance since they knew if they were performing better or worse. And the people at the end of the assembly line had the consistent results they wanted and were therefore less frustrated. Who would have thought there would be so many benefits from just a little bit of feedback? And it’s so easy to provide!
Might this be happening in your business? What are your different processes and what are the different points of feedback you may not be giving to your team members? Who are the people that at the beginning of your “assembly line” that could benefit from some feedback that would then allow you to be happier with some better results? If you can’t seem to figure it out contact us and we will definitely help you out.
Coach Shoenmaker is a frequent contributor to the ActionCOACH.com blog. To learn more about his coaching offer see his website https://seanschoenmakers.actioncoach.com/
Reason #1: Different styles and methods of business coaching don't work for everyone
It's important to be honest with yourself and conduct a realistic assessment when it comes to business coaching. Though business coaching can have many benefits, it might not work for everyone.
Every individual brings their own experiences and values to the coaching dynamic, so results will vary. Additionally, some individuals might need more than just a coach. They might also need specialised knowledge or communication strategies specific to their industry or target audience. Below are a few key factors to consider:
Reason #2: There is no clear focus or vision (talk about time dedication here too)
cIt's important to be honest with yourself and conduct a realistic assessment when it comes to business coaching. Though business coaching can have many benefits, it might not work for everyone.
Business coaching is an effective tool for developing a clearer focus and vision for growing your business. A good coach will help you to take a comprehensive look at your strengths, weaknesses, and available resources that can be used to reach those goals. They will also help you draw up action plans with step-by-step instructions to get there.
By providing honest feedback and being patient throughout the process, a business coach can make sure that you’re on the right track. This will enable you to set realistic milestones and tasks.
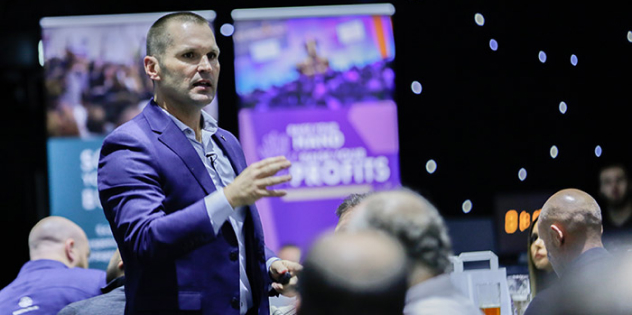
These tasks may need dedicated time outside of coaching sessions. For example, a coach might help a client develop a marketing strategy or implement new systems for managing employees. However, if the client does not have enough time to devote to these tasks outside of coaching sessions, progress will likely stall.
Both the coach and the client must have enough time available to reflect on past experiences, brainstorm new solutions, and test out different strategies. If either party is rushed or distracted during coaching sessions due to other commitments or obligations, they may struggle to fully engage in this process.
Effective business coaching also requires a commitment to regular meetings and ongoing communication. If either the coach or the client does not have enough time to dedicate to these meetings, progress may be slow or nonexistent.
It's important to recognise that business coaching is an ongoing process that takes time to yield results. While some clients may see improvements after just a few sessions with their coach. Others may need months or even years of consistent effort before they begin seeing real changes in their businesses.